Help & Advice Articles, Videos and How-to-Guides
Filter Articles
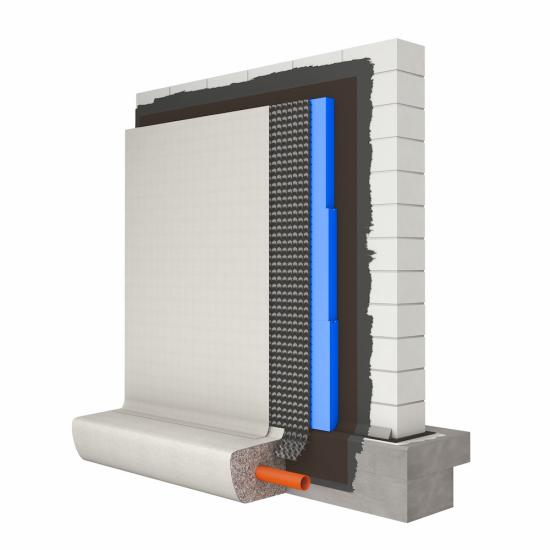
External Waterproofing - How To Guide
When a property is under construction, you need a way of keeping water out of the building. With structures that are earth-retaining (in direct contact with ground), there is always the risk that moisture can penetrate and cause damage to the building. In particular, this applies to new build cellars, basements and any below ground structures.
The rise of local water tables means that there is often increased hydrostatic pressure exerted on earth-retaining walls. External waterproofing should therefore always be considered as it is the first line of resistance.
When working on a new build basement, you should use an external waterproofing system to reduce or block the passage of water through your external earth-retaining walls.
External waterproofing systems use moisture-impervious coatings and Geodrain membranes to block and divert the hydrostatic pressure that may be acting against a structure. This reduces the risk of water ingress and failure of any internal waterproofing systems. The overall risk of any water ingress into the basement or cellar is greatly reduced.
We would always suggest when using an external (also known as Type A) waterproofing system that it is combined with either an internal cavity drain membrane (Type C) or an integral waterproof structure (Type B). This gives you two forms of waterproofing under BS 8102:2022, which is often required for insurance purposes.
We have covered the internal waterproofing of basements extensively elsewhere, so will now look at the external waterproofing of cellars and basements. In this guide, we take you through the external waterproofing methods and how they work.
Waterproofing New-build Basements and Cellars
Why Do I Need External Waterproofing?
The ultimate goal is a dry internal environment in your basement or cellar. Any walls in direct contact with the earth may experience hydrostatic water pressure. You therefore need to effectively deal with this pressure to stop water from entering the structure.
You can tank the basement structure using conventional barrier tanking. However, if tanking is subjected to sufficient hydrostatic pressure, then any slight defect will be exploited. Also, barrier tanking is generally non-maintainable, which increases the risk of failure over time. A complete external waterproofing system plus an internal cavity drain membrane is the best option for mitigating risk.
Environment
It is important to consider your environment when installing a new-build basement. This will require a professional who can analyse the soil type, ground drainage, the presence of any potential contaminants (PermaSEAL Geodrain cavity drain membrane is resistant to all chemicals normally found in the ground), and the height of the water table. These should be considered in light of the intended use of your basement.
External Waterproofing Systems
With external waterproofing systems, we recommend combining a primary waterproofing layer and a secondary drainage/protection waterproofing layer, along with a priming stage for the PermaSEAL Self-Adhesive Membrane option.
Priming
In most cases, the first step in external waterproofing is priming. Priming involves applying a specially designed spray to the external structure. This forces the masonry pores to narrow, creating a water-repellent surface. Primers are also designed to chemically bond with the waterproof coating used in the primary waterproofing stage. PermaSEAL PRO MP 2C has the advantage of not requiring a separate product as a primer. Instead, a thin scratch coat of MP 2C is applied.
Primary Waterproofing
Primary waterproofing involves applying a waterproof material directly to the external wall. You should waterproof the substrate with a waterproofing compound such as PermaSEAL PRO MP 2C or PermaSEAL Self-Adhesive Membrane. These coatings and membranes have a high compression strength and are watertight even under aggressive pressure. This is your main waterproof layer.
Secondary Waterproofing Layer – External Membranes
You should install an external waterproofing membrane. This works as a drainage system to quickly remove any water and alleviate hydrostatic pressure against the building. As well as this, the membrane provides a protective layer for the primary waterproofing, especially during the backfilling process. It also acts as a slip membrane as the backfill settles.
These membranes feature numerous studs (like an egg box), which create a cavity. This allows any water to drain freely down the cavity to a land drain or French drain. More information on drains can be found below. The drain channels the water to a suitable evacuation point like a sump chamber with pump, mains drain or a soak away point. The water also passes through a filter (fabric or internal polypropylene layer, often referred to as Geotextile) in the membrane. This prevents fine particles from entering the drainage system and causing problems.
By employing the above external waterproofing system, you have both a primary and secondary waterproofing barrier. By using these methods together, you greatly minimise the risk of defects.
Both methods are also highly flexible, giving you confidence that as the building settles or if it moves in the future that the external masonry waterproofing will move with it and remain watertight.
Drainage
In this section, we will look at the drainage options for new build basements in a bit more detail. With your external waterproofing system, you will need to provide a drainage system to remove water to a sump chamber or soak away point.
Land Drains and French Drains
To further protect your basement from water ingress, you should install a land drain, sometimes referred to as a French drain. These are laid around the perimeter of the basement below the top level of the slab.
In essence, you have a trench around the perimeter, which contains a perforated pipe covered with gravel or crushed stone. Water that hits the external surface, runs down the membrane then passes through the gravel and is then safely removed to a sump chamber, mains drain or soak away. The gravel that surrounds the land drains should be wrapped in a geotextile membrane to stop fine sediments and debris from blocking the pipe. Access points and jetting points should also be included for annual maintenance.
Sump and Pump
The Sump and Dual Pump system is designed to remove ground water from cavity drain membrane systems as detailed above. They usually combine a sump chamber and a pump, often two pumps in case one of them fails. Systems should also include a shut-off valve so that you can service the pumps. A battery-back up also makes sense should electrics fail.
You can purchase our PermaSEAL Basement Sump and Pump System which has all you need or read more about how the sump pump system works.
How to Install an External Waterproofing System
The following three stages should be followed when installing a PermaSEAL external waterproofing system:
- Priming: PermaSEAL PRO MP 2C does not require a primer. Start by fully wetting out the substrate and applying a thin scratch coat of MP 2C to the damp surface.
- Primary waterproofing: Apply two coats of an external waterproofing coating such as PermaSEAL PRO MP 2C using a brush or trowel method.
- Secondary waterproofing layer: Cover the surface with Geodrain cavity drainage membrane.
- Cap off the open top edge of the membrane using Geodrain Capping Strips.
Products
PermaSEAL PRO MP 2C
PermaSEAL PRO MP 2C is a multi-purpose, highly flexible waterproof coating. It is perfect for waterproofing below ground structures that require a system that can cope with potential movement. MP 2C is bitumen-free and offers excellent crack bridging. With very strong adhesion to mineral substrates and high-pressure resistance, it can bond to old bitumen surfaces and is the ideal product for external waterproofing applications. Learn more about PermaSEAL MP 2C here.
PermaSEAL 8 Geodrain
PermaSEAL 8 Geodrain external waterproofing membrane allows water to freely drain through the filter fabric into the cavity.
Permagard - over 35 Years of Basement Waterproofing Experience
If you have any questions about external waterproofing or basement waterproofing in general, just get in touch. One of our technical advisers will be more than happy to discuss your situation or provide a quote on 0117 982 3282. For our contractors, we offer PermaSEAL's Geodrain membrane in bulk with significant savings.
Further Reading